100分の1ミリの誤差も見逃さない金型職人の“不屈の精神”とは?【ガンプラ開発陣インタビュー】
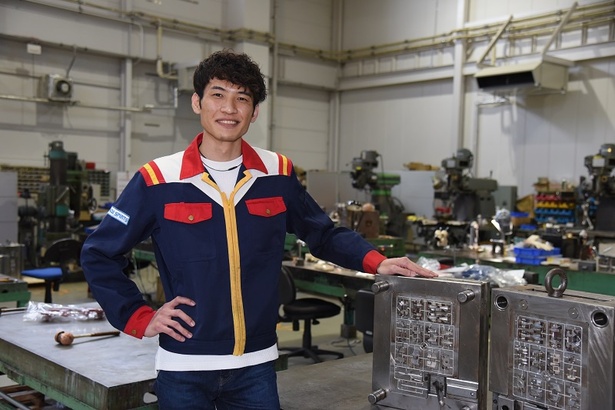
40年以上の歴史を誇り、国内はもちろん、海外でも絶大な人気を誇るガンダムシリーズのプラモデル(通称:ガンプラ)。同商品にクローズアップしたイベントやテレビ番組に加え、“製作技術”世界一を決めるコンテスト「ガンプラビルダーズワールドカップ」も定期的に開催されるなど、その人気はとどまるところを知らない。
ウォーカープラスでは、そんなガンプラの“国内唯一の製造拠点”としても知られる、BANDAI SPIRITSの事業所兼工場「バンダイホビーセンター」の取材を実施。企画・設計・金型・原料・成形・デザインというポジションでガンプラ製造に携わる開発陣にインタビューを行った。その模様を全6回の連載形式で紹介する。
第3回となる本稿は、生産戦略チームの中野博貴さんに金型の業務にかける想いや、ガンプラ開発において苦労したエピソードなどを聞いた。
100分の1ミリの傷、ゆがみにも気づける感覚を習得
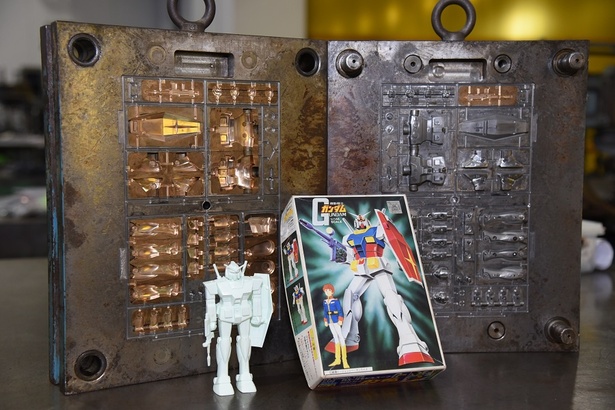
子供の頃からモノづくりが好きだった中野さんは、学生時代にたまたまテレビで見た“バンダイホビーセンターのモノづくり”に興味が沸き、入社を希望したという。金型チームに配属され11年間、金型のメンテナンス業務に従事。その後、成形チーム、生産戦略チームでも経験を重ね、現在は「ランナーや取扱説明書をまとめてパッケージ化する工程」の管理業務を担当している。さまざまな部署でガンプラ開発に取り組んできたことで、自身の視野が広がったことを実感できたらしく、以下のように話す。
「当初は『新規金型技術の開発提案や金型を壊さない量産成形手法』など、金型経験者視点の提案が中心でしたが、今では多角的に、ガンプラ開発の在り方について考えられるようになりました。生産視点で『型構造をもっとこうした方が、生産効率や品質を上げられるんじゃないか?』というフィードバックも、金型チームに対し積極的に行っています」
今では全部署と幅広くやり取りを行うポジションに就く中野さんだが、やはりもっとも経験の長い金型業務に対しては、思い入れも強い模様。続いて、金型チームの業務内容についてお聞きしたところ、金型製作やメンテナンスを、高い技術力を持った金型メーカーと一緒に取り組んでいるという。
ちなみに、プラモデルにはごく稀にバリ(樹脂を成形したときに、意図しない場所にできてしまう突起のこと)が生じることがあるが、これは金型に樹脂を流し込んで形を整える際、どうしても起きてしまう成形不良の一種だという。ひとつの金型で何度もくり返して成形を行ううちに、細かいカスが取れずにこびりつき、その上からさらに樹脂を流し込むことで金型が欠けたり、歪んだりしてしまい、そこに細かい隙間ができることが原因だとされている。
こうした事態にならないよう、入念にメンテナンスをし、もしもバリが発生した場合は即座に修正するそうだが、そのほとんどが100分の1ミリほどのごく小さな傷の補正で、顕微鏡で見ながらの作業になるという。新旧さまざまな金型を修繕してきたという中野さんだが、古い金型ほどメンテナンスには技術が要るそうで、その理由を以下のように話してくれた。
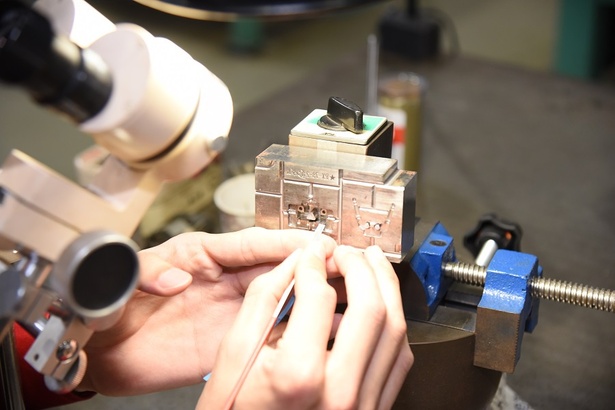
「最初期の金型は40年以上も前に作られたもので、それを今でも使い続けているのですが、当時は今と違って3DCAD(3Dのモデリングソフト)のない時代です。最近の金型ならどんなに壊れても、データがすべて残っているので機械加工に頼って修正できますが、最初期のものは手描きの設計図しか残っていないので、それを見ながらの手作業となり、感覚で直すしか方法がありません」
このような理由もあり、金型チームのスタッフは機械を使うだけでなく、手作業でも修正を行うことが多いという。「一人前になるには10年かかる」とも言われているそうで、慣れてくると金型の表面を指でなぞるだけで、100分の1ミリ、2ミリのゆがみにも気づくようになるのだとか。
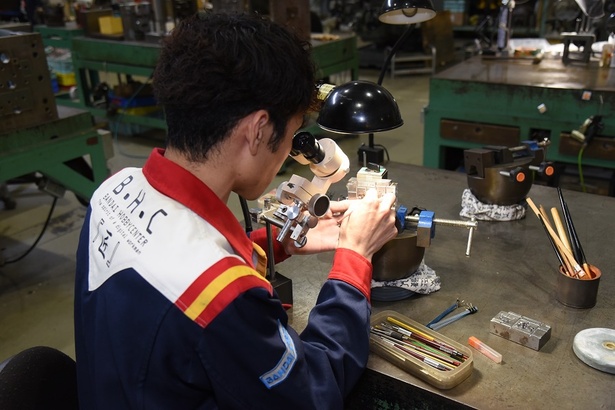
中野さんは金型チームに所属してから5年目のある日、その感覚に目覚めたそうで、「覚醒とでもいうんでしょうか。いつもと同じ作業をしていたら急に、ほんのわずかな違いがわかるようになったんです。何の前触れもなく、本当に『あぁ、こういうことだったんだ』ということがわかって。不思議な感覚でしたね」と話してくれた。
挑戦し続ける精神が、ファンも納得のクオリティを生み出す
仕事に対するやりがいについて「金型の業務は技術・経験を求められて非常に難しいが、やりきったときの達成感は格別」と話す中野さん。金型の製作・メンテナンスにおいて、特に印象に残っているのは、初めてメンテナンスを担当した「HGUC1/144 ゼータガンダム」だそうで、「なかなかうまくいかず、テスト成形をしては調整…という工程を何十回もくり返してようやく完成に漕ぎつけたガンプラなので、あの時の達成感は忘れられないですね」とのこと。
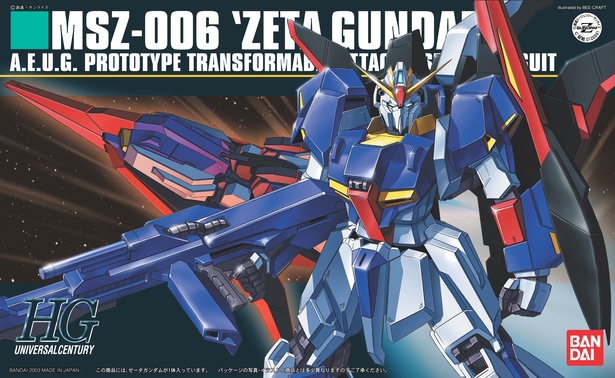
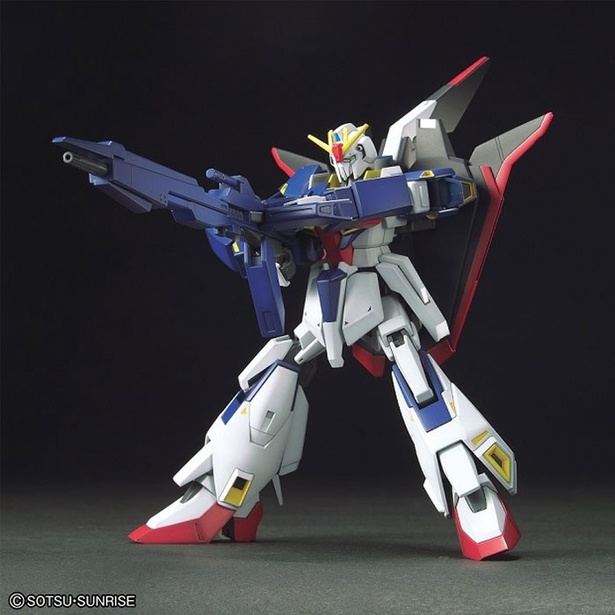
そうして経験を積んでいき、いくつもの金型を手掛けるようになってからも、困難な業務はたびたび発生したという。その中でもひときわ大変だったガンプラは「HGUC 1/144 ネオ・ジオング」だそうで、金型を製作した際のエピソードを聞かせてもらった。
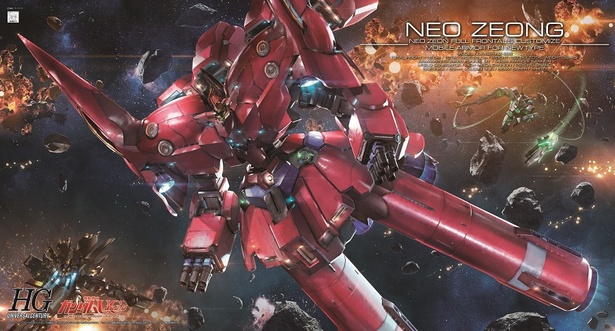

「かなり大きめのガンプラなんですけど、商品が大きいということは、金型はさらに大きくなる…ということで、1商品のために巨大な金型を30型以上、製作することになったんです。また、ただ単に各パーツを大きくすればいい…というわけではありません。通常のガンプラと同じ感覚で関節部位のギミックなどを調整すると、緩くてきちんと固定できなかったりします。今までとは全く違った調整が必要ですし、いつもよりはるかに大きいものを30型以上、毎日調整する必要があります。そうした調整をする日々が1カ月以上続いたので、無事に完成して発売されたときは、これまで以上に自分の技術にも自信を持てるようになりました」
トライし続ける精神を持つことが、金型製作のいちばん大切な資質
こうした金型チームでの経験に加え、成形や生産に関しても知識を深め、現在の業務にあたる中野さん。多くの部署を経験したからこそ、各チームの要望や、それに対する最適な対応も理解できるようになったそうで、やり取りの際は「真摯に話を聞き、それぞれの部署が納得する最適案を提示する」ことを心掛けているという。
また、金型の製造に関しては独りよがりにならないよう、ユーザーから届く声も大事にしているという。同社のプラモデルは、そのクオリティの高さがSNSなどでも称賛されているが、その一方で、「ユーザーは常に新たな価値(技術)を導入した商品を求めている」ことも、寄せられるコメントからひしひしと感じているという。現状に満足せず、技術的に攻めた商品を作り続けることも強く意識していると話す。
具体的にどのような技術開発に取り組んでいるのか? 最後に、中野さんのモノづくりに対する姿勢と併せて、意見を聞かせてもらった。
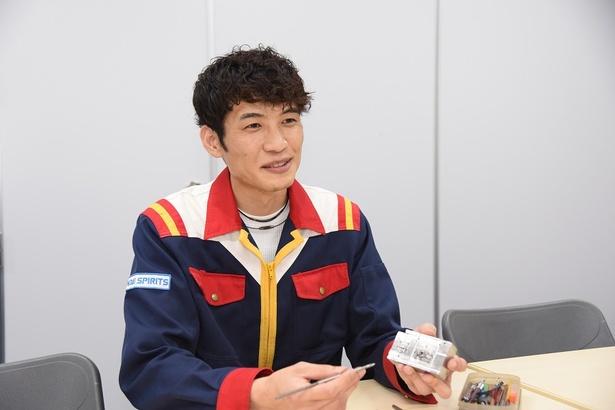
「技術開発にあたり、固執した考えが一番の障壁となるので、ヒントを得るためにも普段の生活の中で樹脂製品は金型構造をイメージしながら見ますし、異業種の製品構造など、常に情報にアンテナを張るように意識しています。
そもそもの話になるのですが、ランナーは商品ごとにすべて形が異なるので、『過去の商品でこういう加工、こういう調整をしたから、今回もそれで行こう』といった前例が通用しないことが多々あります。当然、金型は毎回、形が違ってきますし、成形機が変わると、樹脂の流れ方も変わってくるので、まったく同じ環境、同じ技術で新商品を作り出すことは絶対にできないんです。だからこそトライアルをくり返し、すべての方法を試して、それでもダメなら、さらに新しい方法を見つけ出す。これは無理だ、ダメだといって、今ある技術の中で何とかしようとするのではなく、トライし続ける精神を持つことが、金型製作にはいちばん大切な資質だと考えています」
※商品の写真・イラストは実際の商品と一部異なる場合がございますのでご了承ください。
取材・文=ソムタム田井
(C)創通・サンライズ