精度と効率を両立した成形で、関わる全員の想いをファンに届ける「品質を保つのは成形担当の腕次第」【ガンプラ開発陣インタビュー】
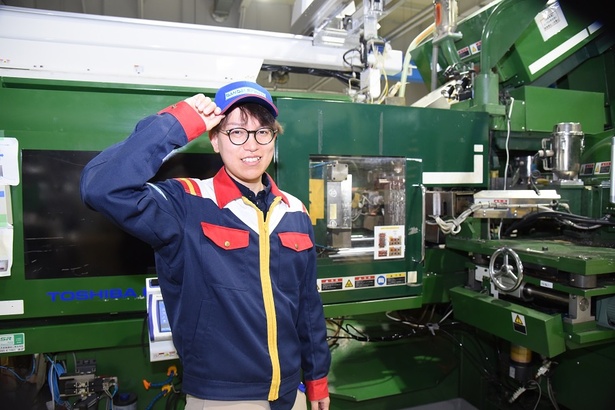
40年以上の歴史を誇り、国内はもちろん、海外でも絶大な人気を誇る『ガンダム』シリーズのプラモデル(通称:ガンプラ)。同商品にクローズアップしたイベントやテレビ番組に加え、“製作技術”世界一を決めるコンテスト「ガンプラビルダーズワールドカップ」も定期的に開催されるなど、その人気はとどまるところを知らない。
ウォーカープラスでは、そんなガンプラの“国内唯一の製造拠点”としても知られる、BANDAI SPIRITSの事業所兼工場「バンダイホビーセンター」の取材を実施。企画・設計・金型・原料・成形・デザインというポジションでガンプラ製造に携わる開発陣にインタビューを行い、その模様を全6回の連載形式で紹介する。
第5回となる本稿は、成形チームの佐野翔紀さん。その業務内容や、ガンプラ開発において苦労したエピソードなどを聞いた。
金型と射出成形機の相性を見抜き、最適な成形プランを実現
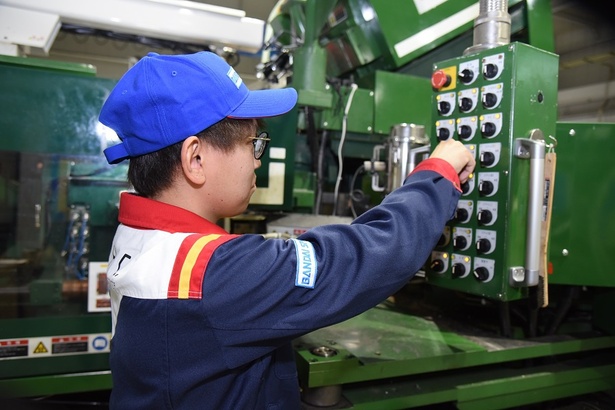
もともとは工業部品を取り扱うメーカーで射出成形機を扱い、生産ラインの構築にも携わっていたという佐野さん。その経験を活かしてBANDAI SPIRITS入社後も金型や成形機を扱いつつ、数字面についても考える…という業務を担当されているそうだが、そもそも“成形”とは、プラモデル開発においてどのようなポジションになるのか?まずは主な業務内容について聞いた。
「端的にいうなら、“材料を金型に入れてランナーを作る仕事”です。射出成形機に金型をセットして、そこに加熱し溶かした材料を流し込み、冷やして固めることで、皆さんが普段見ているランナーが出てくる。というプラモデルの量産を担当しているポジションになります」
ちなみに射出成形機とは、“プラスチック成形の王様”と呼ばれるほど製造業界内では広く使われている機械とのことで、取り扱う際は材料を流す“温度” “速度” “圧力”等の条件設定が必要になり、安定して量産する為には一定の技術が必要になるのだとか。また、季節や天候に合わせた温度管理が重要だという。
「よく、“プラモデルの材料である樹脂はわがままな生き物”と表現されるのですが、とにかく環境の影響を受けやすい物質なんです。弊社の場合、ランナーは3ミリ~5ミリの厚みになるんですけど、ちょっとでも温度コントロールを間違えると、プラスチックがうまく固まらず、ちゃんとした形状にならなくて。逆に温度を高めに設定してしまうと、今度はバリという不良が出てしまうので、その辺りのバランス感覚といいますか、温度に関しては特に気を使っていますね」
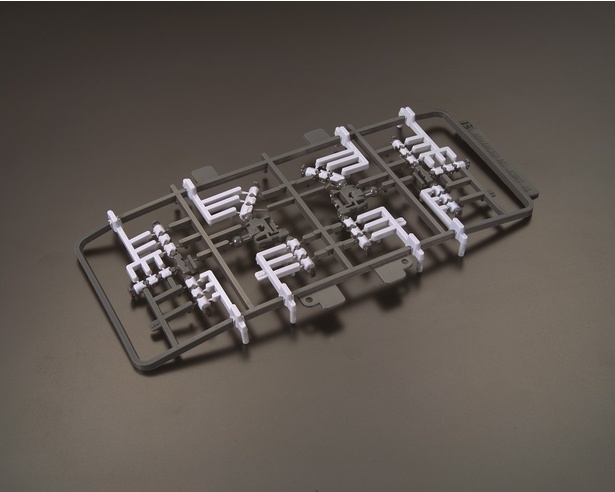
そうした射出成形機の取り扱いに加え、佐野さんの業務には「物流・生産戦略チームとこまめに受注量を確認し合いながら、機械を効率よく動かし、期日までに製品を納める」という、成形プランのコントロールも含まれている。こちらの作業における大変な点や、苦労されている点についても話してもらった。
「たとえば、HGシリーズというブランドの場合、1商品のパッケージに5~6枚のランナーが入っているという構成になります。そうなると、ランナー分の金型が必要になるわけですが、じつは金型には、“最適な温度が微妙に違う”など、一つひとつに特徴があるんです。この金型には成形機A、この金型には成形機Bといった感じで、金型ごとに相性のいい成形機は異なるので、それを見極め、最適な生産ラインを組み立てる…というところも、成形チームにおける重要な業務のひとつですね。また、金型は金属で出来ていますが、非常にデリケートです。成形する際に一歩扱いを間違えると苦労して作った金型を壊してしまい、金型チームの努力を無駄にしてしまう為、扱いには細心の注意を払っています」
ここまでのお話で、「高品質の商品を効率的に量産する」事こそ、成形チームの主な役割であることが理解できた。そのようなガンプラ成形の難易度の高さを実感する一方、楽しいと感じたエピソードがあったという。
「特に印象に残っているのは『RG 1/144 ジオング』の手のパーツです。このパーツはインサート成形という特殊な技術が使われており、ランナーから切り離しただけで指の関節が動くようになっています。前職でもインサート成形は経験したことが無く、初めて成形条件を出したのですが、何層かに重ねて成形をしている都合上、樹脂を入れるタイミング、量、温度、すべてのバランスが重要で少しでも間違えると、製品形状が欠けてしまったり関節がくっついて動かなくなってしまい、うまく成形が出来ません。解決方法がわからず悩んでいたところ、先輩が『類似製品の条件を参考にしたら?』と「PG 1/60 アストレイレッドフレーム」の手のインサートパーツの条件を見せてくれて、『材料を射出する速度をもう少し早くしたらうまく行くかも』とアドバイスをもらいました。その結果、試行錯誤を経てようやく安定した成形を行うことが出来ました」
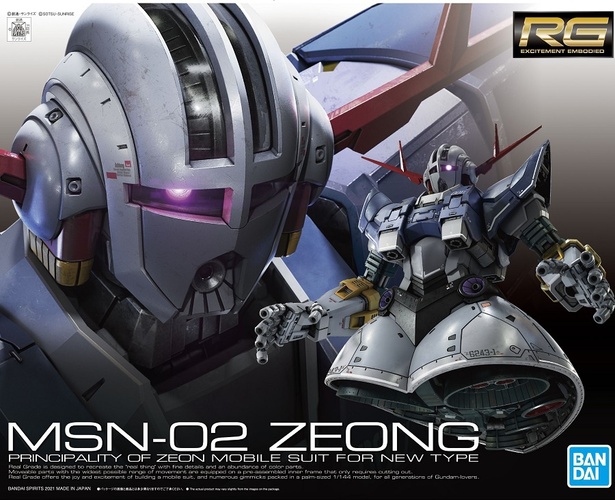
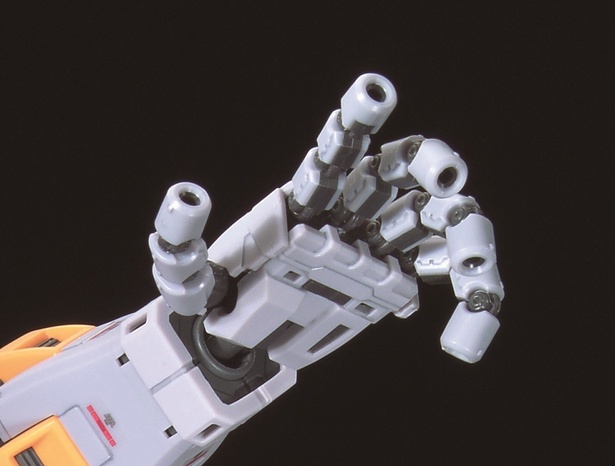
「私の場合、成形は前職でも経験していたため、『少しやってみれば出来るだろう』という自信もありましたが、わからない点は経験豊富な先輩方に相談する事がとても大事だな、と学ぶことが出来ました。BANDAI SPIRITS特有の4色成形はコントロールが非常に難しく、時間が経つと温めた材料がどんどん溶けてしまうので、1色成形の4倍の仕事量を1色成形とほぼ同じ時間で行う必要があります。これは取り扱いに慣れているスタッフであっても、ハードルの高い作業です。先輩方もモノづくりが好きな方ばかりで、長年に渡り培ってきた拘りのあるノウハウがデータとして残されているので、それらを吸収し、出来る仕事が増えていくことに、とてもやりがいを感じます」
ファンとの交流を通して、さらなる品質の向上を目指す
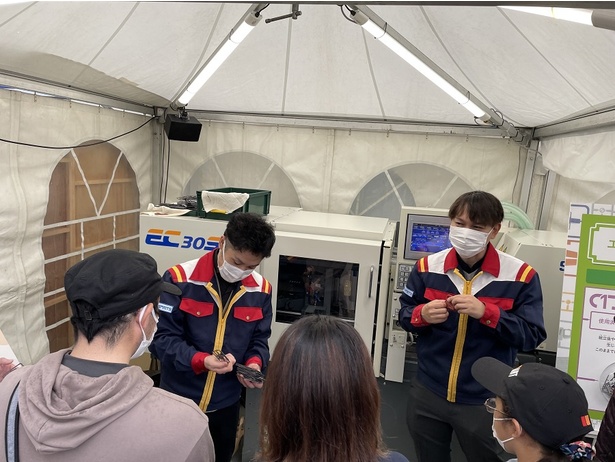
こうして日々、高品質な商品の量産および、商品の生産体制構築に取り組んでいる佐野さんだが、ここ数年はファンとの交流の機会も大切にしているそうで、そこで得た知見をもとに、プラモデルのさらなる品質改善にも取り組んでいるという。最後に、“ファンとの交流”の詳細を話してもらった。
「『PLAY!PLAY!PLAMO!』という、弊社が行っているプラモデル作りを体験できるイベントでは、会場まで射出成形機を持ち出して、ファンの目の前でプラモデルを作り出すという催しを実施しました。そうした場で、直接、商品に対するご意見をいただけるのはありがたいですね。我々は日頃から全精力をかけてモノづくりに取り組んでいますが、それが作り手だけの思いになってしまい“自分達の考えは正しい”とか、“プラモデルはこうあるべき”みたいな凝り固まった考えにならないようにという点は常に気を付けています。こうしたイベントに参加して、ファンの方々からリアルなご意見を頂戴したり、喜んでくださっている姿を目の当たりにすることでさらにモチベーションが上がったりします。そうやってコミュニケーションを取りつつ、よりよい形で皆様にお届けするということを、今後も続けていきたいと考えています」
取材・文=ソムタム田井
(C)創通・サンライズ